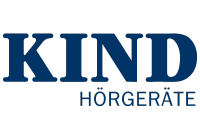
2 Minutes Faster and a Reduction in the Error Rate: KIND relies on NIMMSTA Smart Watches 🇬🇧
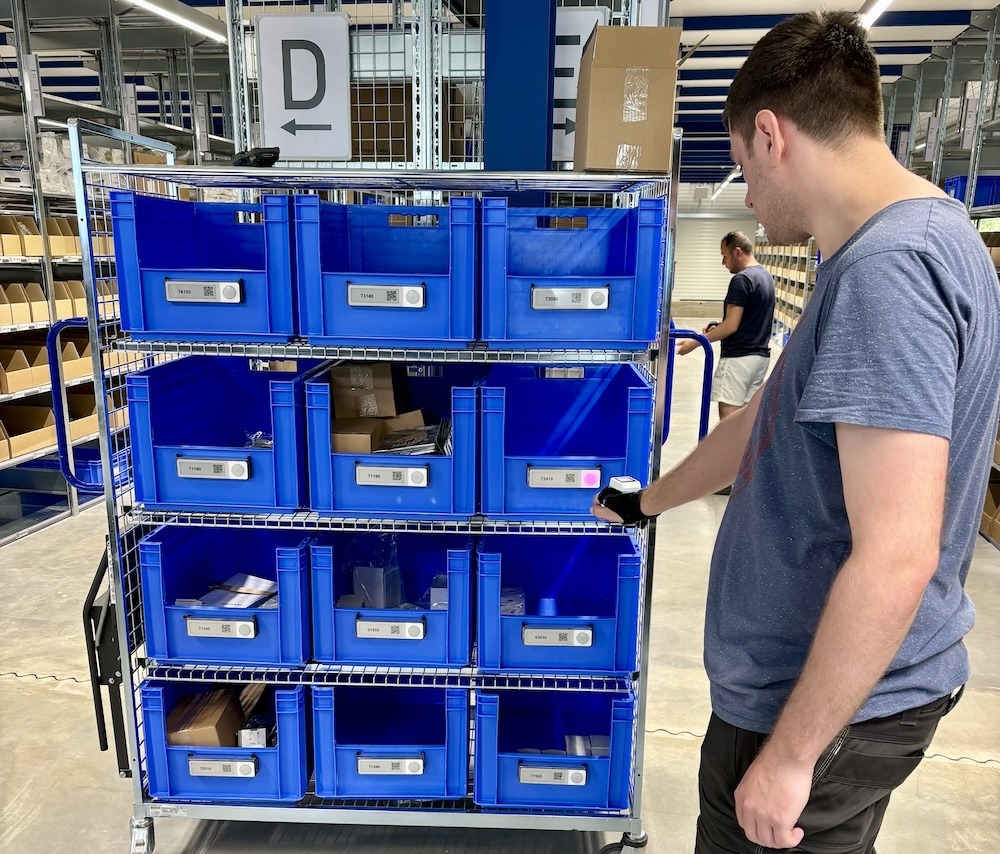
Industry
Retail
Use Case
KIND GmbH & Co. KG, a leading hearing acoustics and ophthalmic optics company, was faced with the challenge of optimising its warehouse processes. Thanks to the introduction of NIMMSTA Smart Watches and the support of the engomo digitalisation platform, KIND was able to make its picking processes significantly more efficient. The switch to single-stage picking led to considerable time savings, a reduced error rate and improved processes.
Results
One-step picking with NIMMSTA saves logistics specialists up to 2 minutes per order and reduces the error rate. The process guides them step by step, eliminates double counting and speeds up workflows. New employees can use the application immediately without extensive training.
Products
NIMMSTA Smart Watch
''The combination of NIMMSTA and engomo has improved our warehouse processes enormously. The increase in efficiency and reduction in errors are impressive and our employees can work much faster and more precisely.''
Jens Feil
Floormanager Lager & Logistik at KIND
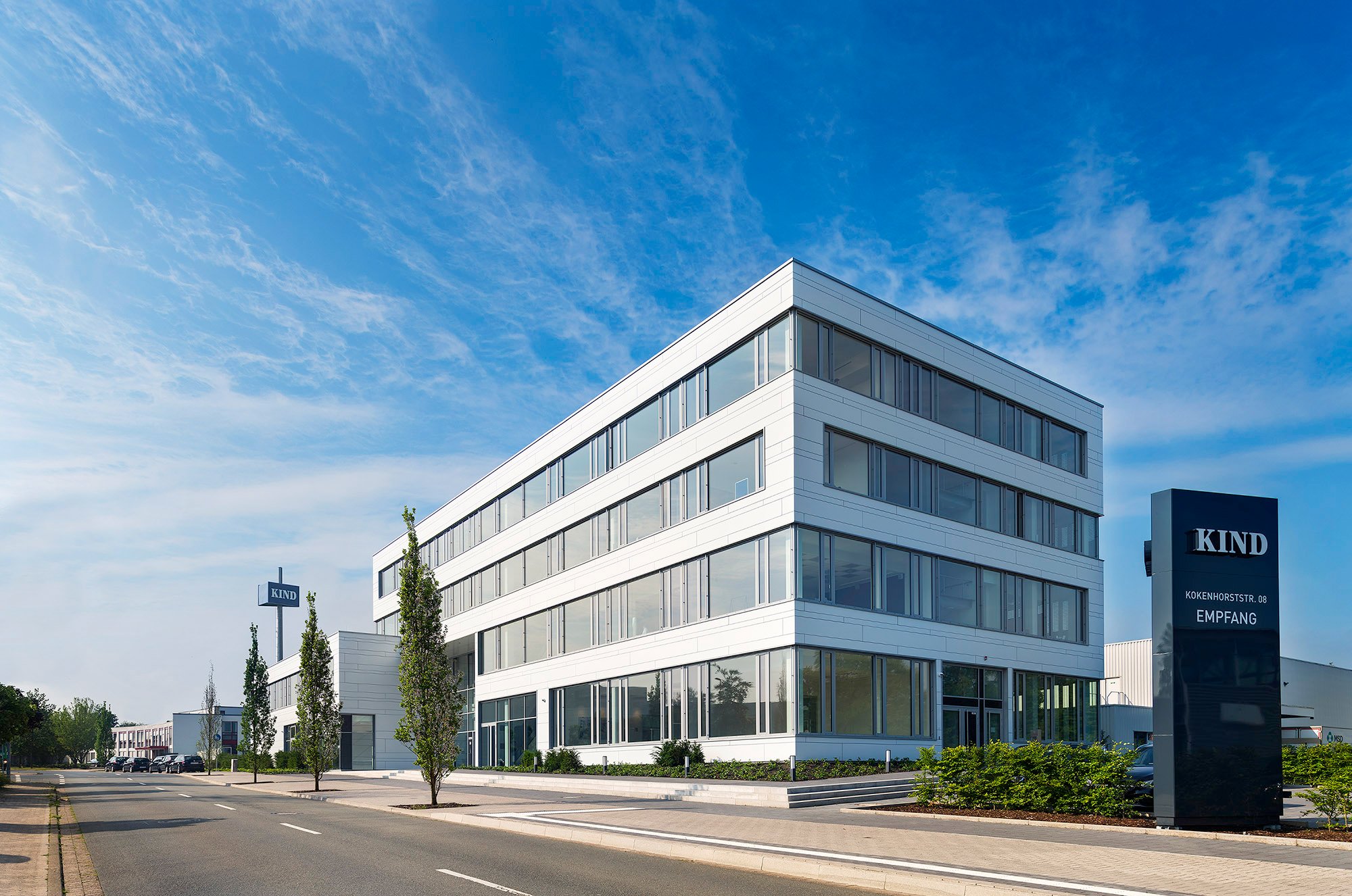
About KIND
KIND was faced with the challenge of optimising its warehouse processes. With over 750 speciality shops, more than 3,500 employees worldwide and a growing portfolio of products, the warehouse at the main site in Großburgwedel was reaching its structural limits. The previous two-stage picking processes led to bottlenecks and a high error rate, which impaired efficiency and accuracy. In the first stage of the picking process, the maximum quantity required for all speciality shops was taken and placed in the picking trolley. In the second stage, the goods were then distributed to the individual boxes that corresponded to the orders of the speciality shops.Optimisation of processes
With the expansion into the ophthalmic optics market and the increasing number of articles and variants, new solutions and technologies were investigated. In addition, narrow aisles made manoeuvring and the simultaneous use of picking trolleys difficult. The storage areas and box sizes were also no longer sufficient. Together with Jörg Murawski from delivers IT, an external project manager and consultant who has been supporting the ERP processes at KIND for over 10 years, the new processes were defined and the best software and hardware solutions were selected.
With the construction of a new logistics centre, KIND decided to switch from two-stage picking to single-stage picking. Covering an area of over 2500 square metres, KIND now uses NIMMSTA Smart Watches with engomo as middleware. The pick positions are generated by the ERP system Microsoft Dynamics AX.
Use of the Smart Watches
In the new logistics centre, the picking trolleys are pre-equipped with twelve boxes, each of which corresponds to an order for a specialist shop. Thanks to the direct connection to the ERP system, engomo takes all information from Microsoft Dynamics AX and displays it on the touch display of the NIMMSTA Watch.
In the first step, the boxes are scanned in a sequence specified on the Smart Watch and thus assigned to the corresponding speciality shop.
The Smart Watch then directs the logistics staff to the appropriate storage locations with precise instructions. Scanning the correct location is signalled with a green light and a vibration pattern. If an incorrect storage location is detected, the watch reports the error back via vibration and a red light. The feedback function has significantly reduced the error rate. The logistician then receives the quantity of the item to be picked via the display. Each box on the picking trolley is equipped with an LED. The LED of the box into which the picked items are to be placed flashes.
Serial number-based processes are also supported; in this case, the logistician is notified of an additional scan check. If an item is not available in the required quantity, a numeric keypad can be opened on the display and a quantity correction can be made. engomo plays this information back directly and the picking list is adjusted in the ERP system. This procedure maintains the process flow and massively improves the overall data quality. The process is finalised via a button. The process described is repeated until all picks for this item have been completed. The logistician then receives a request to go to the next storage location.
2 minutes faster per order
Thanks to the successful implementation of the NIMMSTA Watches and the low-code application of engomo, KIND has brought state-of-the-art technology into the warehouse and realised optimised, efficient processes. The switch to single-stage picking with these technologies has eliminated double counting, reduced the error rate and significantly accelerated processes. This saves two minutes per order. These improvements give KIND a significant competitive advantage in hearing acoustics and ophthalmic optics. In the future, KIND plans to develop further areas of application for these technologies in order to further increase efficiency in the warehouse and beyond.
Related case studies
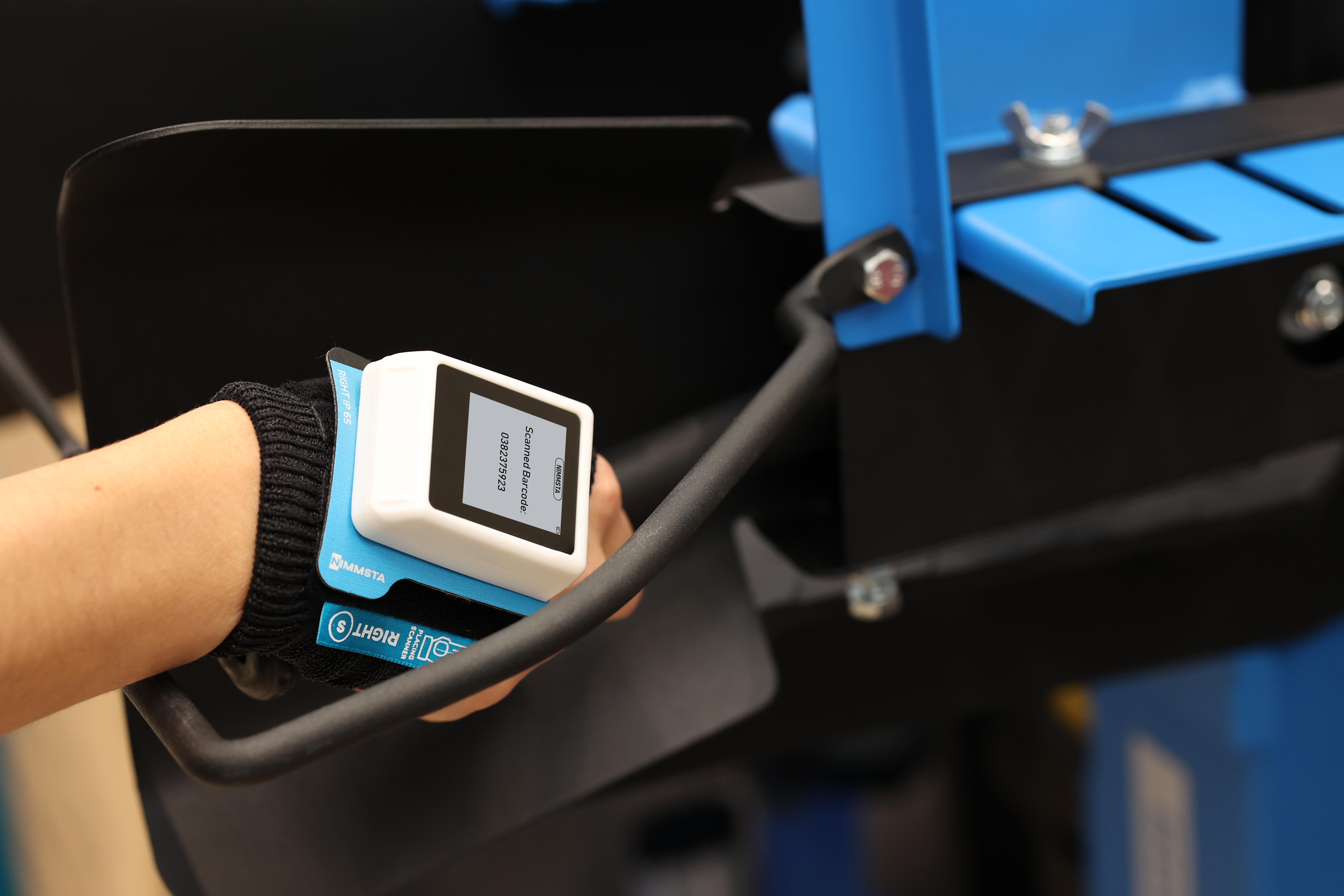
NIMMSTA begeistert REWE DORTMUND mit erheblichen Prozessoptimierungen 🇩🇪 Täglich werden 250 Tonnen Frischware präzise und effektiv kommissioniert
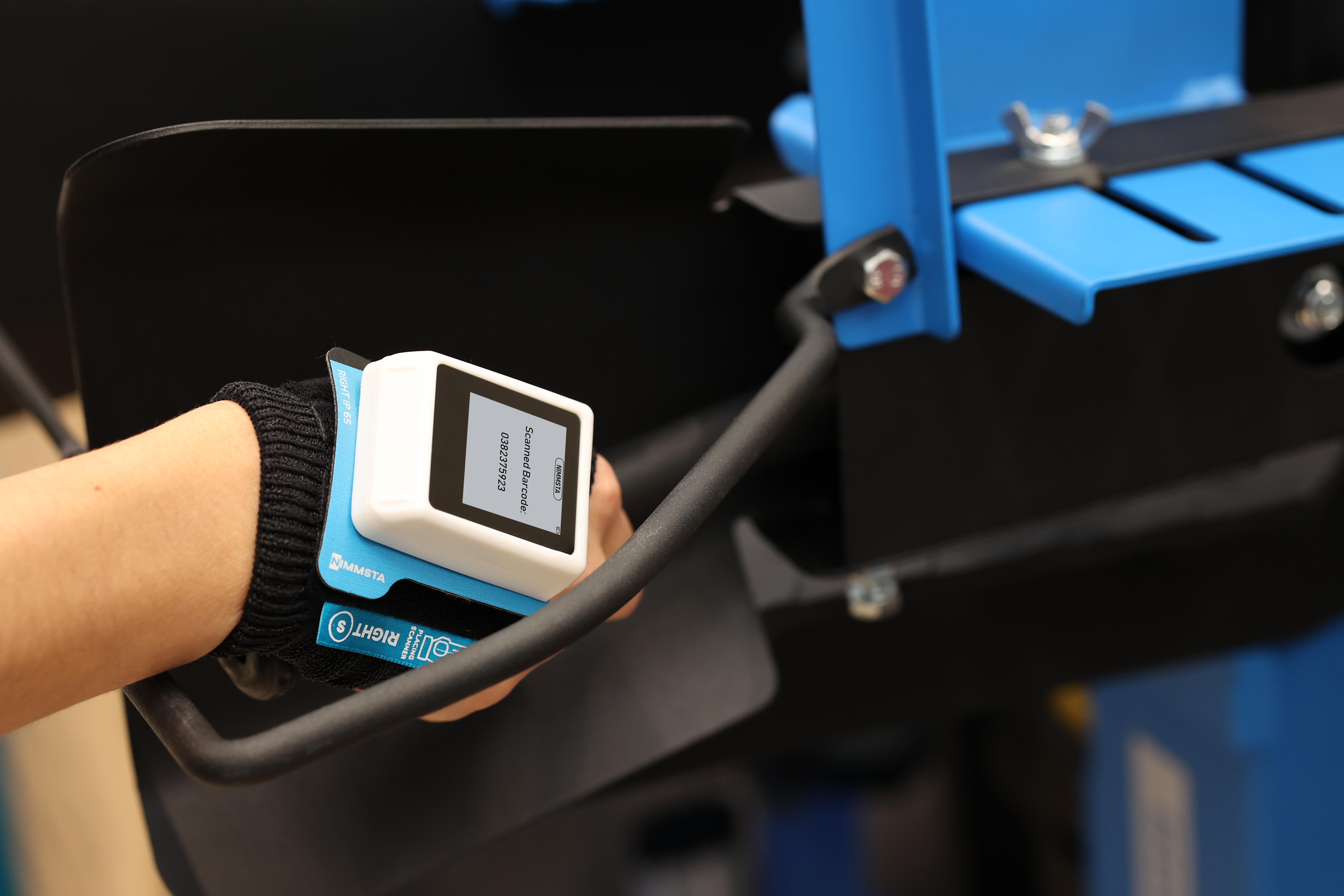
NIMMSTA delights REWE DORTMUND with significant process optimisations 🇬🇧 250 tonnes of fresh products are picked precisely and effectively every day
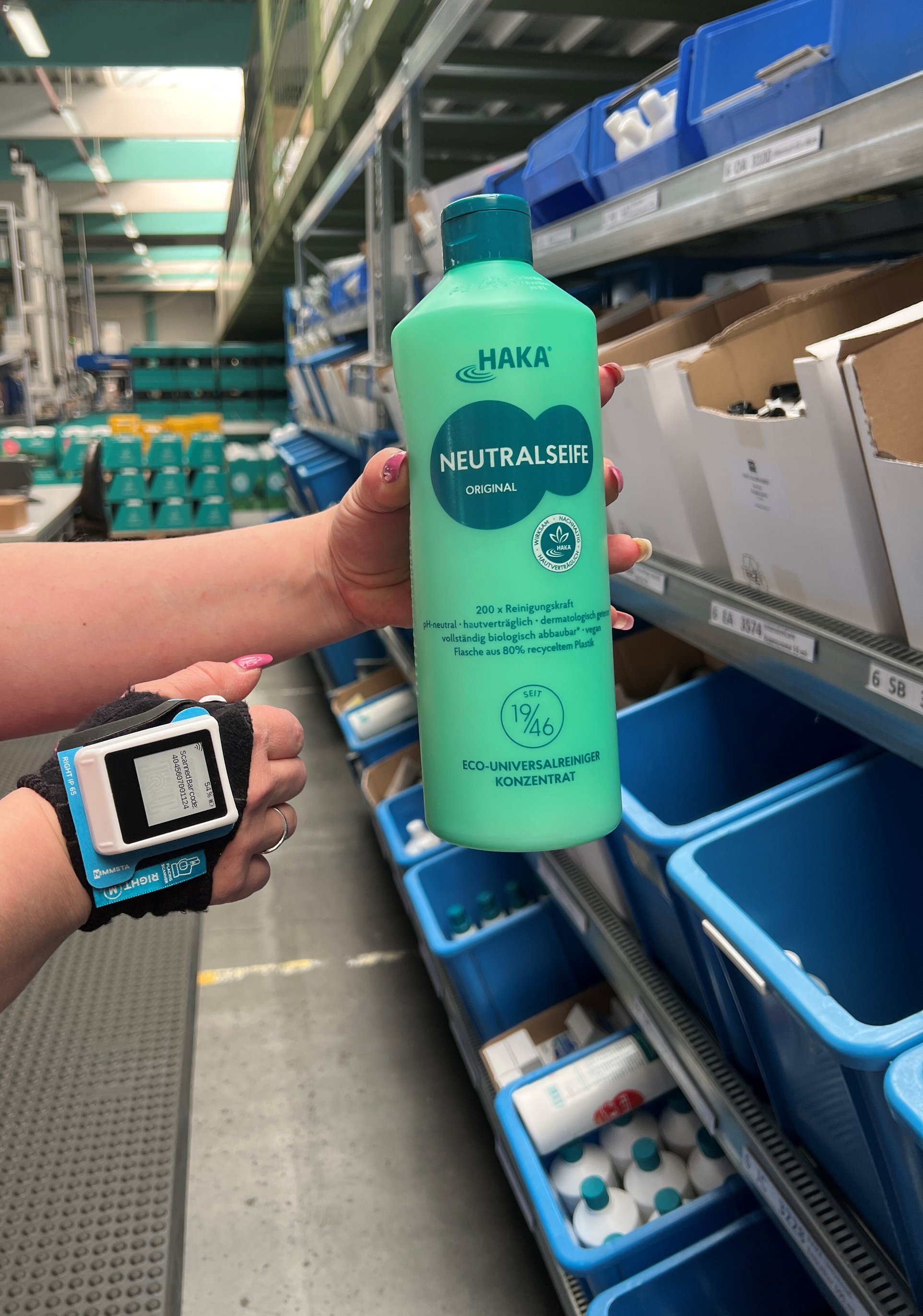