.png?width=625&height=438&name=Logos%20f%C3%BCr%20Customer%20Success%20Stories(1).png)
12 seconds less per picking process - MÜLLER | DIE LILA LOGISTIK optimizes picking processes with the NIMMSTA Smart Watch 🇬🇧
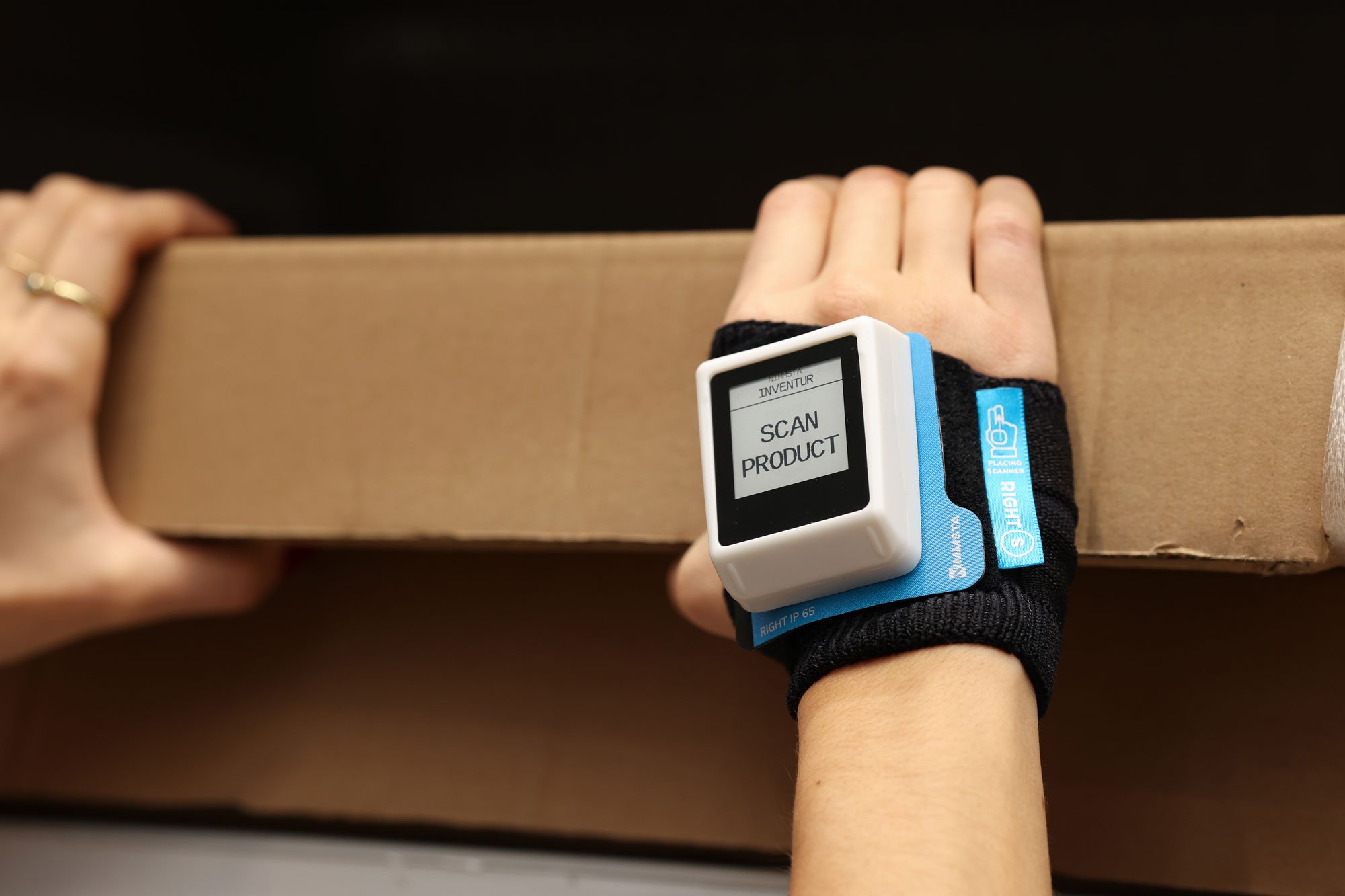
Industry
Services
Herausforderung
Process optimization of the picking process by eliminating search times.
Ergebnisse
The first calculative as well as empirical results show a process streamlining since picking with the NIMMSTA wearables. The following optimizations can be observed at Lila Logistik: More efficient work processes, reduction of process times, 12 seconds less per picking process, less damage to the goods, lower error rate, weight, size and scanning performance is described as very good by the employees.
Produkte
NIMMSTA Smart Watch
„We succeeded in securing efficiency and an increase in performance with NIMMSTA along the entire pickingprocess chain.“
Carolina Glinka
Prozessmanager at Lila Logistik
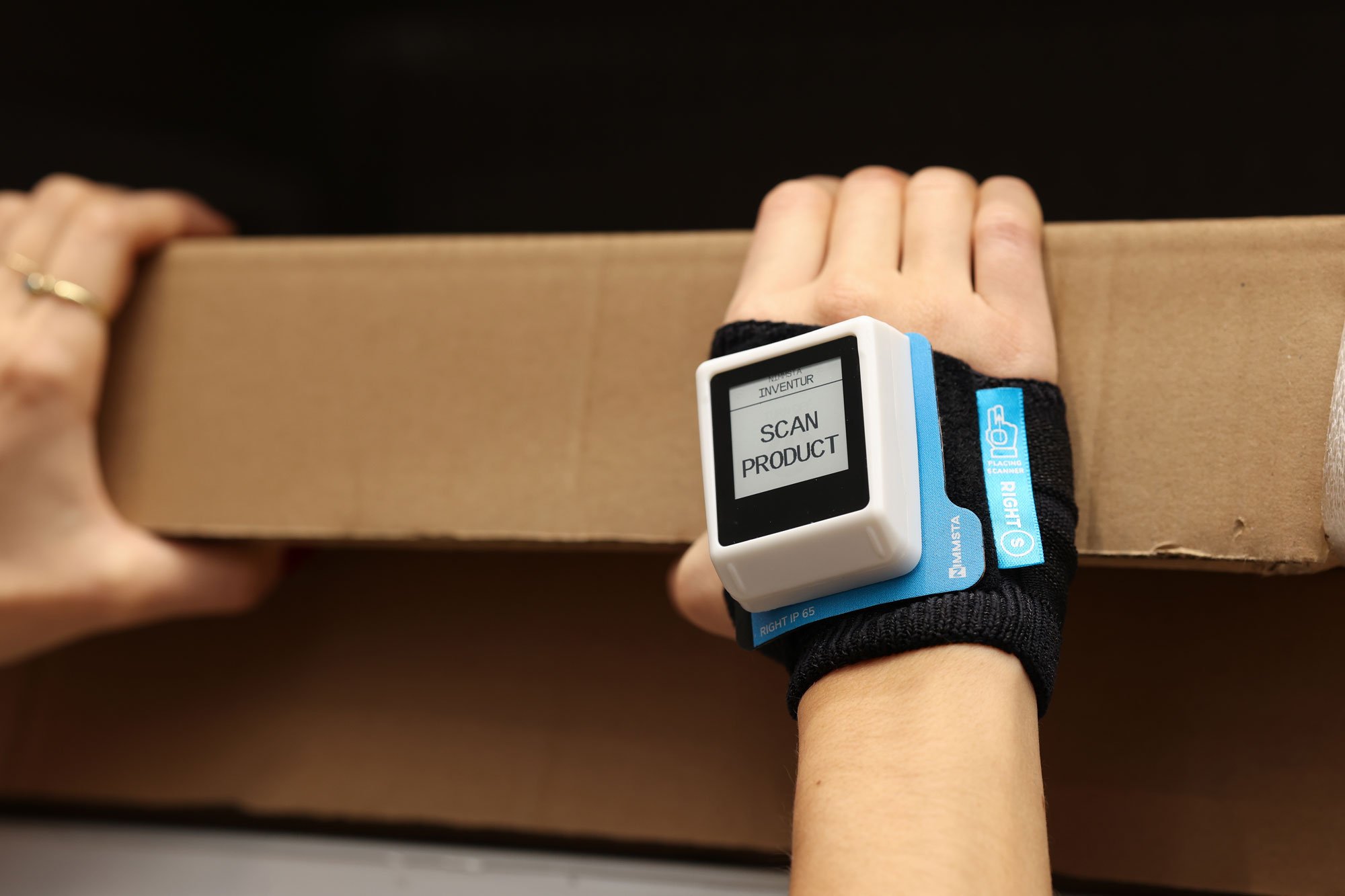
About MÜLLER, DIE LILA LOGISTIK
MÜLLER | DIE LILA LOGISTIK is a nationally and internationally active logistics service provider offering all relevant functions of contract logistics. Since its founding in 1991, they have grown into a listed company with around 1,700 employees. The broad service portfolio includes the services Deliver, Warehouse and Assembling as well as Real Estate with real estate areas for service production.Challenge
Logistics is the core competence of Lila Logistik, so they are continuously looking for
improvement potential and future-oriented technical solutions.
In order to be able to carry out their picking processes faster and free-handed, the company was looking for new equipment. The decisive factor was the „free hands“ option. In the relevant area, Lilia Logistik picks foams, heaters and covers for well-known automotive manufacturers. The employees need two hands for the picking process. The original MDE device had to be put down on the picking cart after each scan in order to be able to grab the large parts. The permanent picking and placing process during the loading of the picking cart costs an undesired amount of time, which the company wanted to eliminate.
Solution
After a short test phase, the logistics service provider decided to use the innovative Smart Watch from NIMMSTA. The decision was made in favor of NIMMSTA due to the following aspects, among others:
• Freehands option
• More cost-effective than other manufacturers
• Dynamic and solution-oriented company
For more than a year, Lila Logistik has been using the BASIC version of the NIMMSTA
wearables, which means that the touch function of the display is currently not activated.
The NIMMSTA wearables are used by the logistics service provider with the „Mid Range“ scan engine, which means that barcode types up to four meters away can be detected without any problems. The Smart Watch is also available in Standard Range (SR), which is ideal for shorter distances. Integration is extremely simple and was implemented in cooperation with Körber, Lila Logistik‘s service provider. The NIMMSTA Core Library is provided free of charge. This was another reason why the decision was made in favor of NIMMSTA.
Experience
Fast and competent customer support is also essential for the company.
important. The cooperation with NIMMSTA is described as very harmonious, friendly
and professional. Initial difficulties with the compatibility of the Smart WAtch and the existing target devices were dealt with quickly and in a solution-oriented manner, and NIMMSTA provided active support at all times until the process worked optimally.
Related case studies
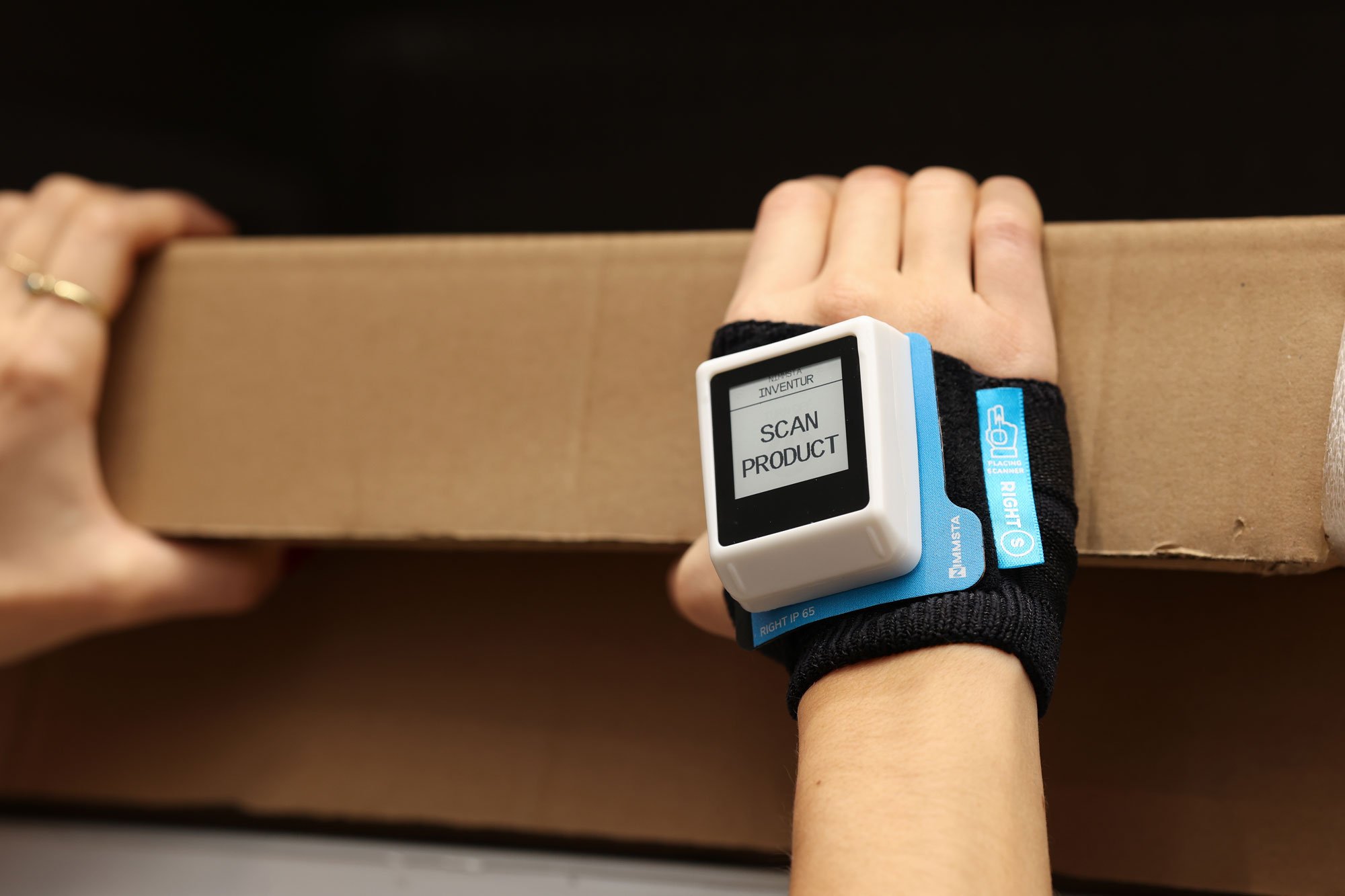
12 Sekunden weniger pro Pickvorgang - MÜLLER | DIE LILA LOGISTIK optimiert Kommissionierprozesse mit der NIMMSTA Smart Watch 🇩🇪
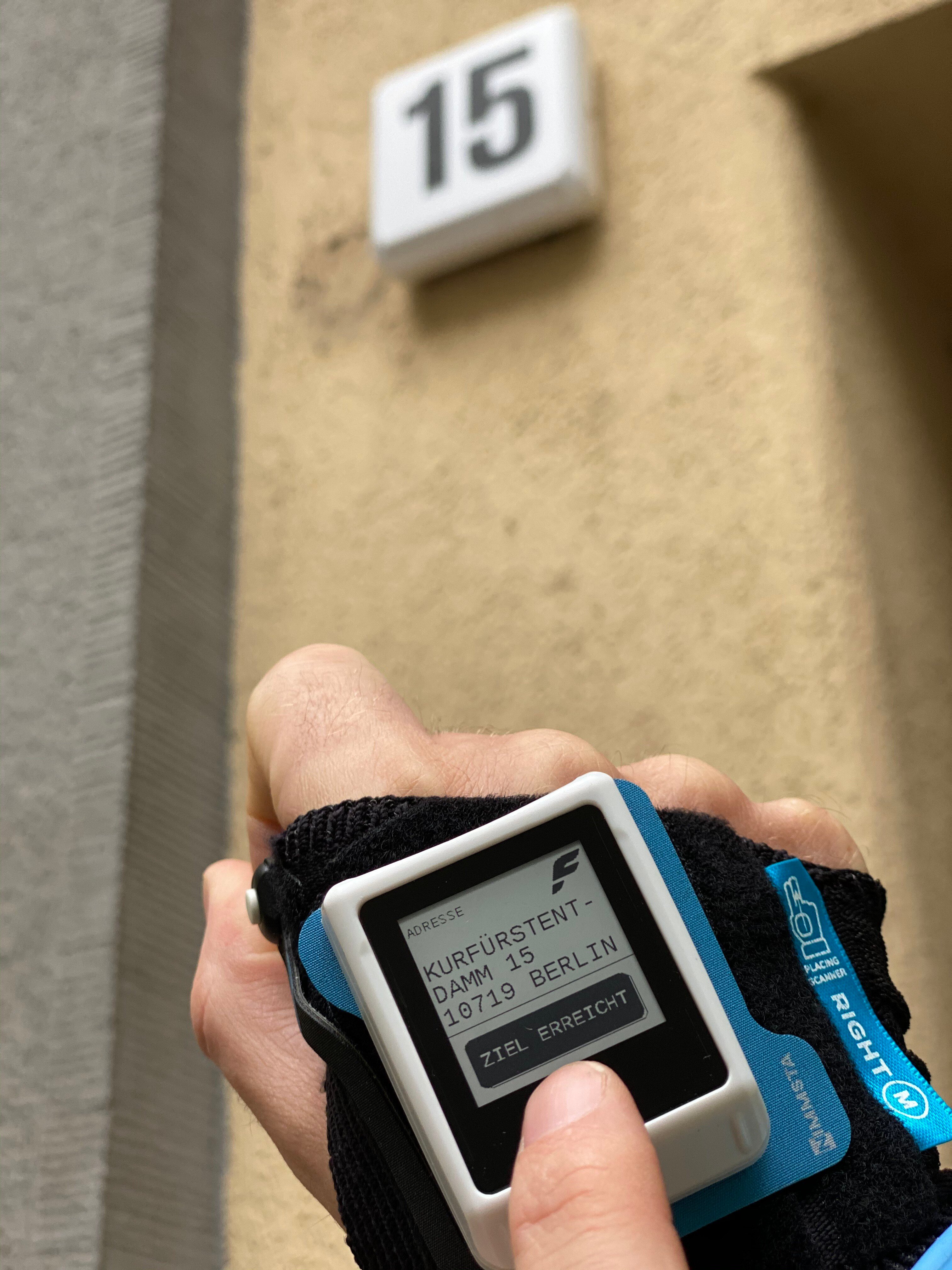
FAIRSENDEN - Smart City Logistiker setzt auf den NIMMSTA Handrückenscanner 🇩🇪
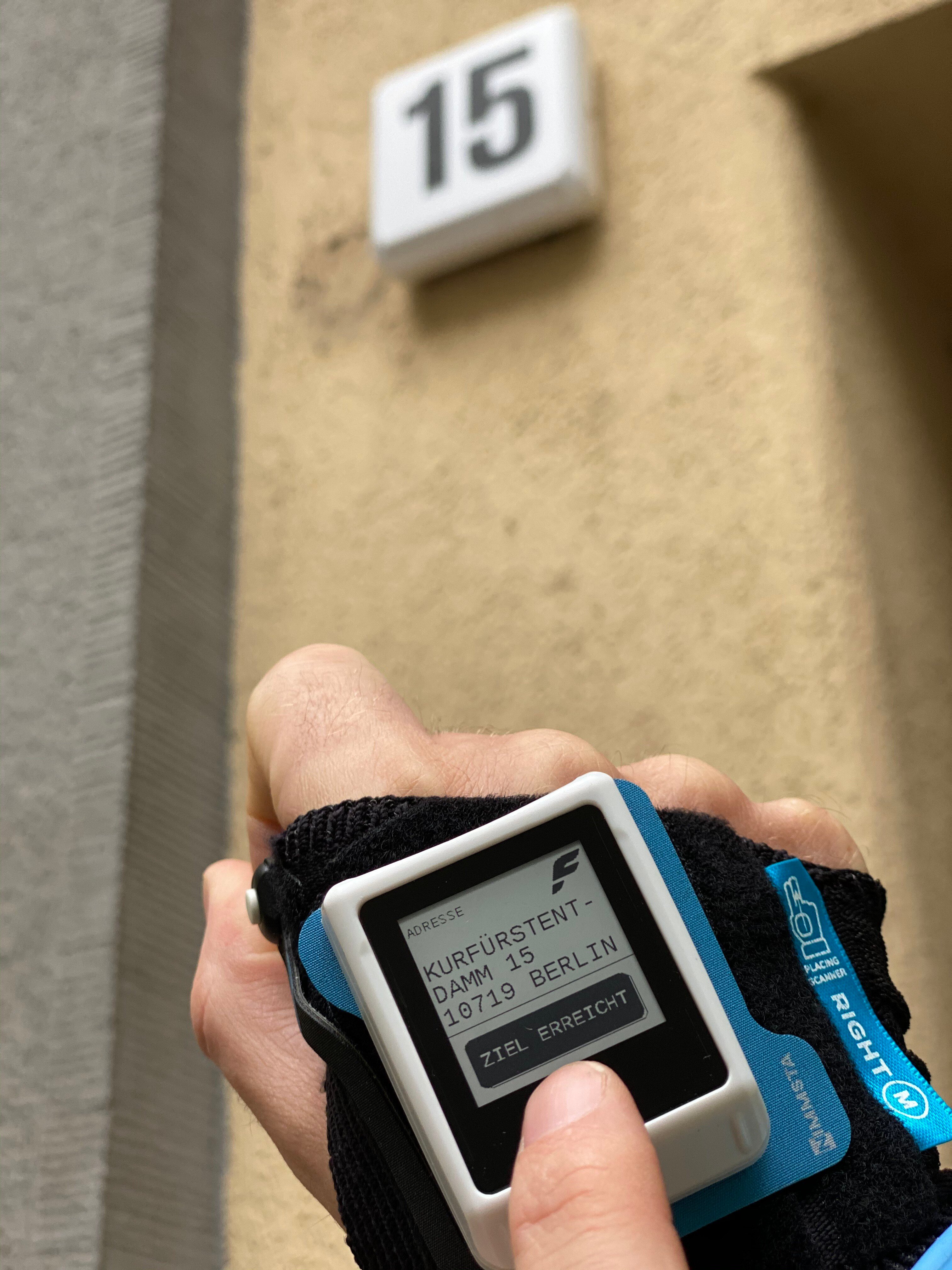